Unique membrane technology recycles waste coolant and antifreeze with high efficiency. The resulting product has already been certified for automotive use by SGS according to the Volkswagen Group standard.
A pilot unit is running at an industrial site on the outskirts of Prague, which could fundamentally change the situation during the recycling of used antifreeze and glycol-containing coolants and, thereby, significantly reduce environmental burden. Waste mixtures are treated here using state-of-the-art membrane technology that can separate pollutants from them with high efficiency. The low-energy method is based on purely physical principles of multi-stage separation without the use of chemicals. “This is the input product”, says Štěpán Kundrt, a technologist at the glycol recycling plant, showing a bottle of murky brown-green liquid. “This is glycol for the first stage of purification”, – the glycol still has turbidity and a tinge of colour. However, the resulting product that flows out of the membrane unit is crystal clear.
DC Solutions s.r.o. used its long-standing know-how in the development of recycling equipment: it is the exclusive distributor of Hydranautics Nitto membranes, one of the world's leading manufacturers. These are special custom-made membranes that are not commonly available. “We have experience and knowledge in the field of membrane separation. Conventional membranes cannot be used for glycol separation”, comments Štěpán Kundrt.
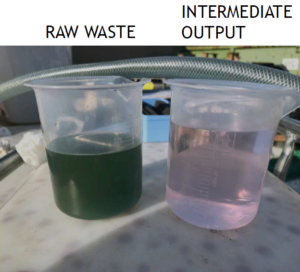
Glycols
The term glycol is used as a more general term for coolants and antifreeze containing either propylene glycol (PEG) or mono-ethylene glycol (MEG). They are widely used in industry, automotive, energy, maritime transport, but also for technical security of buildings or solar systems. In the Czech Republic alone, glycol consumption is estimated at 18,000 m3/year. Since a water mixture containing 40-45% glycol is usually used, we are talking about more than forty thousand m3 of coolants and antifreeze per year. According to statistics, only one percent of this amount is returned for further processing each year. Where the rest went is unclear. However, it would definitely be better for our environment if this waste were managed in a controlled way.
Glycols are toxic substances classified as hazardous waste under catalogue number 16 01 14 N. To date, it is mostly disposed of through the costly process of incineration in hazardous waste incinerators, which is perhaps why so few are officially returned. Currently used recycling plants based on electrodialysis or distillation are operationally quite demanding (high energy consumption) or require complex pre-treatment of the input product. A proportion of the original dyes may also remain in the output, which is limiting for the subsequent use of the recyclate. Therefore, they are not very economically interesting for practice.
Operation
In the RECOL pilot plant the waste liquids are first filtered several times and then fed by a high-pressure pump into a unit equipped with specially manufactured membranes. The product is obtained by repeated removal of pollutants in several steps. “While the clean glycol-water mixture is removed from the system, the contaminated portion is returned to the inlet container”, explains Štěpán Kundrt. “At the end, only the worst of the pollution, which is about 15-20% of the original volume, really remains in the input container. In addition, we get up to 85% pure glycol-water mixtures. The product has the same glycol content as the feedstock, which means we don't lose any active ingredient in the regeneration process”.
The only limitation to the fouling concentration is how quickly the membranes are fouled, as this effectively determines the capacity of the unit between regenerations. “We test the incoming material and if it is very dirty, we save it for the end before regenerating the membrane so that it does not unnecessarily contaminate the system”, explains Štěpán Kundrt. “We have to take care of the membranes. We monitor their performance and capacity depletion rates based on various operating parameters such as pressures and flow rates. They are then cleaned with a special chemical solution and flushed so we can continue”, he adds.
The purified glycol-water mixture is analysed and then made into a new product by adding the necessary additives, dyes or corrosion inhibitors. DC Solutions has obtained certification for this recycled product according to the Volkswagen Group standard for reuse in the automotive industry. “According to our information, we are the only operators in Europe to hold this certification”, says Štěpán Kundrt.
Development
They started working on the device in 2019, having and calculated the process. This was followed by verification at the University of Pardubice, which was significantly slowed down by Covid-19. When the unit first started up in November 2021, it treated approximately 900 litres of heavily contaminated waste coolant from the automotive industry. Over 700 litres of pure glycol solution was recovered for reuse. They now plan to produce a fully automatic unit with a capacity of 100 to 200 litres per hour. “We are able to supply waste processors with fully automated on-call equipment and we can also guarantee to buy back the recycled compound from our facility.” It is important to train the operators of the waste collection and sorting plant, who should be able to perform simple tests, for example, to distinguish between PEG and MEG, which have a significantly different recyclate value and, above all, facilitate the whole recycling process and minimise secondary waste.
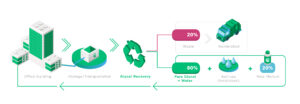
Economics
The price for the disposal of waste mixtures containing glycol in a hazardous waste incinerator is high, last year reaching around USD 550/t. In contrast, the market prices for pure glycol are disproportionately higher, with PEG now selling for USD 3,300 per tonne and MEG for USD 1,400 per tonne, and prices are still rising. The recycling of glycol mixtures and their reuse as a certified product can therefore be very economically interesting.
In addition to the economic gains the new process further offers significant environmental gains: the production of MEG and PEG from non-renewable sources will be reduced and, most importantly, the negative environmental impact of glycol use, which are currently disappearing to unknown destinations, will be significantly reduced.
“In general, this technology is positively received. It not only has economic potential, but also significant environmental benefits and is a further step closer to the so-called circular economy. We are therefore convinced that there will be interest in the equipment and we will soon see our units in operation around the world”, concludes Štěpán Kundrt.
Jarmila Šťastná